Unlocking the Secrets of Manufacturing HDPE Pipes
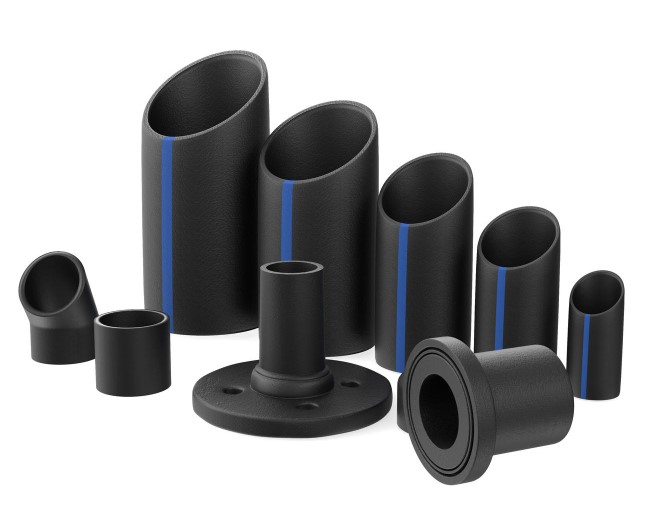
High-density polyethylene (HDPE) pipes are essential components in many industries, from water supply to wastewater management and gas transportation. The manufacturing process of HDPE pipes involves several critical steps to ensure that the final product meets industry standards. This blog post will explore the detailed process of manufacturing HDPE pipes, innovations in the field, and the challenges manufacturers face.
HDPE Pipe Manufacturing Process:
Manufacturing HDPE pipes is a precise and systematic process, which requires the use of advanced technology and high-quality materials. The process is divided into several key stages that ensure the pipes produced are durable, reliable, and efficient for use in various applications.
Step 1. Manufacturing HDPE Pipes uses Raw Materials
The process of manufacturing HDPE pipes starts with the careful selection of raw materials. The primary ingredient is HDPE resin, a high-density thermoplastic polymer. HDPE’s high molecular weight gives it exceptional strength, resistance to corrosion, and the ability to withstand high pressure and temperature. Additionally, manufacturers may add specific additives to improve the pipe’s properties, such as antioxidants, stabilizers, or colorants.
The resin is sourced from reliable suppliers, and its quality is scrutinized to ensure it meets industry standards for strength and durability.
Step 2. Extrusion Plays Key Role in Manufacturing HDPE Pipe
Once the raw materials are selected, the next step in manufacturing HDPE pipe is extrusion. In this stage, the HDPE resin is fed into an extruder, a large machine that heats the material to its melting point. The molten HDPE is then forced through a mold to form a continuous pipe. The extrusion process ensures that the pipe’s diameter and thickness are consistent throughout its length, which is crucial for maintaining the strength and integrity of the pipe.
Step 3. Cooling
After extrusion, the newly formed HDPE pipe needs to cool down to solidify. Cooling is usually done through a water bath or air cooling system, where the pipe is gradually cooled to room temperature. The cooling process is critical in ensuring that the pipe does not warp or develop any defects, which could affect its functionality and lifespan.
Step 4. Measures Quality Control
Quality control is a vital step in manufacturing HDPE pipes, ensuring that each pipe meets the required standards for durability, performance, and safety. Pipes undergo rigorous testing, including checks for pressure resistance, dimensional accuracy, and surface quality. Manufacturers also conduct various tests to ensure the material’s integrity, such as testing for tensile strength and impact resistance. Only pipes that meet these high standards are allowed to proceed to the next stage of production.
Step 5. Packaging and Storage
Once the pipes pass quality control, they are cut into the required lengths, packaged, and prepared for storage or shipment. Proper packaging is essential to avoid any damage to the pipes during transport. HDPE pipes are typically stored in a climate-controlled environment to maintain their quality and prevent exposure to harsh weather conditions that could degrade the material.
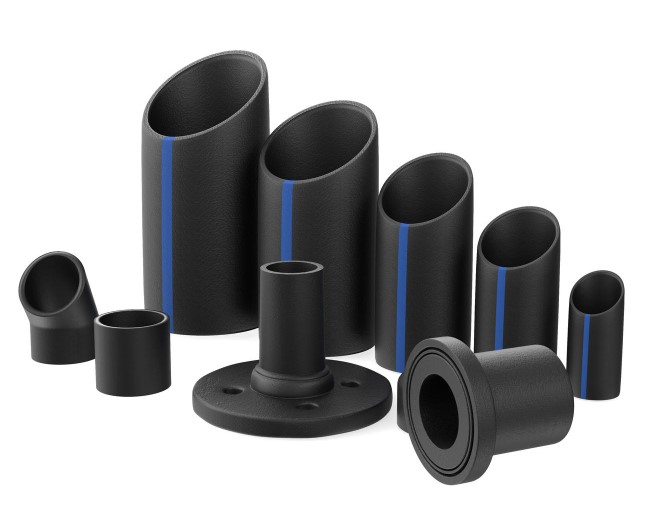
Innovations and Advances
The field of manufacturing HDPE pipes has seen numerous innovations in recent years. Advanced extrusion technologies now allow for the production of pipes with more complex geometries, offering better performance and adaptability to specific applications. Moreover, improved additives and stabilizers enhance the longevity and environmental resistance of HDPE pipes.
Another notable advancement is the development of smart HDPE pipes, equipped with sensors that can monitor the condition of the pipe in real-time. This technology allows for proactive maintenance, reducing the risk of failures and increasing the overall efficiency of the systems in which the pipes are used.
Common Challenges in HDPE Pipe Manufacturing
Although the manufacturing HDPE pipe process has become more advanced, several challenges still persist. Manufacturers face issues such as raw material inconsistency, production defects, and the need for energy-efficient processes. Let’s take a look at some of the main challenges.
Addressing Material Defects in HDPE Pipe Production
One of the key challenges in HDPE pipe manufacturing is addressing material defects. Variations in raw materials can lead to inconsistent pipe quality, affecting performance and safety. It is critical for manufacturers to carefully source and test the raw materials, implementing strict quality control measures throughout the process to minimize defects and ensure the production of reliable pipes.
How to Optimize Efficiency in HDPE Pipe Manufacturing?
Optimizing efficiency in HDPE pipe manufacturing is crucial to staying competitive in the industry. Modern technologies, such as automation and predictive maintenance, can help streamline the process, reduce downtime, and minimize waste. Manufacturers are also looking for ways to lower energy consumption and reduce the environmental impact of their operations. By adopting lean manufacturing principles and investing in advanced equipment, companies can optimize the manufacturing HDPE pipe process, improving both production speed and product quality.
Regulatory Standards and Compliance in HDPE Pipe Manufacturing
Compliance with industry regulations is another significant challenge in HDPE pipe production. Manufacturers must adhere to various standards and regulations, such as those set by ASTM, ISO, and the American Water Works Association (AWWA). These regulations ensure that HDPE pipes meet specific safety and quality requirements. Manufacturers must stay up to date with any changes in these regulations and implement the necessary changes to their processes to ensure compliance and avoid penalties.
Conclusion
The process of manufacturing HDPE pipes is complex and requires precision at every step. From selecting the right raw materials to ensuring stringent quality control and meeting regulatory standards, every stage plays a vital role in producing durable and reliable pipes. As innovation continues to shape the industry, manufacturers are continually improving their processes to produce pipes that offer better performance, efficiency, and environmental sustainability. By understanding the intricacies of HDPE pipe manufacturing, businesses and consumers alike can make informed decisions about their pipe systems, ensuring they choose the best possible products for their needs.
Also Read: Choosing HDPE Pipes: A Complete Guide